„Warum nutzen wir das denn nicht?“ Dieser Satz war der Grund warum jetzt in der Feinmechanik-Werkstatt der Dienststelle Hamburg ein 3D-Drucker steht.
Eines Tages stand ein Kollege bei mir in der Werkstatt und zeigte mir stolz ein kleines Kunststoffbauteil. Wie sich herausstellte, handelte es sich um ein kleines Blinkergehäuse für das heimische Moped. Hergestellt mit einem selbst zusammengebauten 3D-Drucker für den privaten Einsatz. Eine Idee war geboren.
Schnell war klar, dass ein 3D-Drucker eine sinnvolle Erweiterung zum konventionellen Maschinenpark der Feinmechanik-Werkstatt sein kann. Am Anfang war die Vorstellung, dass wir direkt größere dreidimensionale Teile für unsere Modellschiffe würden drucken können. Nach intensiver Recherche der am Markt verfügbaren Techniken und den entsprechenden Druckern relativierte sich jedoch diese Vorstellung. Derartige Geräte sind derzeit noch viel zu teuer, um in der Feinmechanik-Werkstatt Prototypen oder kleinere Serien von Bauteilen zu produzieren.
Zur Auswahl standen das FDM-Fused Deposition Modeling Verfahren. Der 3D-Drucker „druckt“ dabei ein verflüssigten Thermoplast durch eine sehr feine Düse auf einen Drucktisch, ähnlich einem herkömmlichen Drucker. Der Unterschied besteht darin, dass nicht nur in der X-Y Ebene (Länge–Breite) gedruckt wird, sondern auch schichtweise in die Höhe (Z). Bei der SLA-Stereolithografie wird das dreidimensionale Objekt durch Aushärtung einer UV-empfindlichen Flüssigkeit (Resin) mit Hilfe eines DLP-Beamers, ebenfalls Schicht für Schicht, erzeugt. Dagegen wird beim SLS-Selektives Lasersintern das Ausgangsmaterial in Pulverform Schicht für Schicht auf eine Bauplattform aufgetragen und mit Hilfe eines starken Lasers beschossen und an den Stellen verschmolzen, an denen das 3D-Objekt entstehen soll. Das SLS-Verfahren ist ein noch sehr teures und auch hinsichtlich der Handhabung und Gefährdung durch die Lasertechnologie aufwendiges Verfahren. Es gibt jedoch im SLS-Verfahren Geräte die es auch ermöglichen Bauteile aus Metall zu sintern.
Für unsere Anwendungszwecke und im Hinblick auf die Kosten entschieden wir uns für einen FDM-Drucker. Seitdem steht das Gerät nicht mehr still.
Der in der Dienststelle Hamburg stehende 3D-Drucker bietet einen maximalen Druckbereich von X350 mm * Y210 mm * Z200 mm. Durch einen zweiten Extruder (Druckkopf) besteht die Möglichkeit auch zweifarbige Bauteile zu verwirklichen. Grundsätzlich wird ein 3D-Modell des zu bauenden Objekts benötigt. Dies kann in der Feinmechanik Werkstatt direkt nach Vorgabe von Ideen oder Zeichnungen mit Hilfe eines Konstruktionsprogramms erstellt werden.
Hat man das Objekt als 3D-Datei vorliegen, muss mit Hilfe eines weiteren Programms, dem „Slicer“, der sogenannte G-Code generiert werden. Der Slicer erstellt ein Programm in dem der Weg beschrieben wird, den der Extruder (Druckkopf) abfahren muss, um das gewünschte Objekt Schicht für Schicht „aufzubauen“. Die Druckzeiten variieren sehr nach Form und Größe eines Objektes. Druckzeiten von über 8 Stunden sind für Bauteile von ca. Länge 100mm * Breite 100mm * Höhe 100mm normal.
Anwendung hat der 3D-Drucker schon reichlich gefunden. Es wurden unter anderen neue Glaskolbenhalter für das geotechnische Labor der BAW-DH, ein Belüftungssystem, sowie verschiedenste Halterungen, Gehäuse und andere Prototypen gedruckt.
Der 3D-Druck hat Einzug in die BAW erhalten. Er kann die mechanische Arbeit im Bereich drehen und fräsen von Kunststoffen nicht ersetzen. Der Druck bietet aber im Bereich des Prototypings ,beim Einzelteilbau oder bei Kleinserien die Möglichkeit einer neuen Denkweise bezüglich Fertigung, Bauteilform und technischer Machbarkeit in unserer Feinmechanik-Werkstatt.
Bei Fragen, Ideen und Wünschen können sich Kollegen gerne an mich wenden.
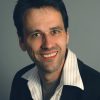
Verfasst von Nico Korbel
Als Mitarbeiter im Technischen-Betriebsdienst der BAW - Dienststelle Hamburg arbeite ich als Feinmechaniker in der Versuchswerkstatt. Meine Hauptaufgabe ist die technische Unterstützung der Referate und die Fertigung von Sonderbauteilen für die Versuchsaufbauten und technischen Anlagen.